この事例で
ご導入いただいている製品
ご導入いただいている製品
- iNetSec FC カタログ
- 今すぐダウンロード!
PFUテクノワイズ株式会社(以降、PTW)は、板金加工からプリント板ユニット製造、それらを元にしたBTO(Build to Order)組立までを一貫して行う製造工場であり、PFUにおけるものづくりの拠点である。
そのPTWでは、過去にネットワークトラブルが発生し、その原因究明に半日を要したことがあった。そうした苦い経験を契機に工場内の機器とネットワーク構成の "見える化" に取り組んだ。これにより、異常発生時の機器の特定や影響範囲をタイムリーに把握することが可能になり、生産業務への影響を最小化できるようになった。
この "見える化" を支えているのがiNetSec FCである。
そのPTWでは、過去にネットワークトラブルが発生し、その原因究明に半日を要したことがあった。そうした苦い経験を契機に工場内の機器とネットワーク構成の "見える化" に取り組んだ。これにより、異常発生時の機器の特定や影響範囲をタイムリーに把握することが可能になり、生産業務への影響を最小化できるようになった。
この "見える化" を支えているのがiNetSec FCである。
ネットワーク障害が発生、
生産ラインが半日停止!
「工場内でネットワーク障害が発生。その原因となった機器の特定に半日かかった。機器を特定するまでの間、必然的に生産ラインの停止を余儀なくされたーー」。
これは架空の話ではなく、2018年に実際にPTWで起こったことである。
工場にとって、生産ラインを停止することは、"工場が止まる" ことを意味する。出荷の遅れだけにとどまらず、金銭的な損失、場合によっては、お客さまや取引業者からの信頼感の喪失など、影響は深刻だ。
当然ながら、PTWでも「止めないための対策」は実施していた。生産設備の管理の徹底はもとより、過去に発生したトラブルの状況を記録したり、工場内の機器の接続関係を示すネットワーク構成図を作成することで、異常発生時の影響範囲を予測したり、といった具合だ。
では、なぜ、原因究明に半日も時間がかかったのか?
工場にとって、生産ラインを停止することは、"工場が止まる" ことを意味する。出荷の遅れだけにとどまらず、金銭的な損失、場合によっては、お客さまや取引業者からの信頼感の喪失など、影響は深刻だ。
当然ながら、PTWでも「止めないための対策」は実施していた。生産設備の管理の徹底はもとより、過去に発生したトラブルの状況を記録したり、工場内の機器の接続関係を示すネットワーク構成図を作成することで、異常発生時の影響範囲を予測したり、といった具合だ。
では、なぜ、原因究明に半日も時間がかかったのか?
工場特有の問題がそこにあった
当時の状況について、製造技術部の泉氏に話を聞いた。
「PTWでは、早い段階から製造品質および生産性向上のための取り組みを進めてきました。例えば、組立の効率化・平準化を狙いとした『組立支援システム』の導入、製造工程全体の効率向上を目的とした『製造支援システム』の導入等を段階的に行ってきました」
「当初はスタンドアロンでの運用も見られましたが、その後、IoT化の進展もあり、"ネットワークでつなぐ運用" が主になっていきました。接続される機器の多様化に加えて、自社開発の各種管理システムも含めて複雑につながっていました。こうした中で、あのトラブルが発生したのです。ネットワークの特性もあり、ある機器の不具合の影響がシステム全体に及んだ結果、ラインも停止してしまいました」
「PTWでは、早い段階から製造品質および生産性向上のための取り組みを進めてきました。例えば、組立の効率化・平準化を狙いとした『組立支援システム』の導入、製造工程全体の効率向上を目的とした『製造支援システム』の導入等を段階的に行ってきました」
「当初はスタンドアロンでの運用も見られましたが、その後、IoT化の進展もあり、"ネットワークでつなぐ運用" が主になっていきました。接続される機器の多様化に加えて、自社開発の各種管理システムも含めて複雑につながっていました。こうした中で、あのトラブルが発生したのです。ネットワークの特性もあり、ある機器の不具合の影響がシステム全体に及んだ結果、ラインも停止してしまいました」
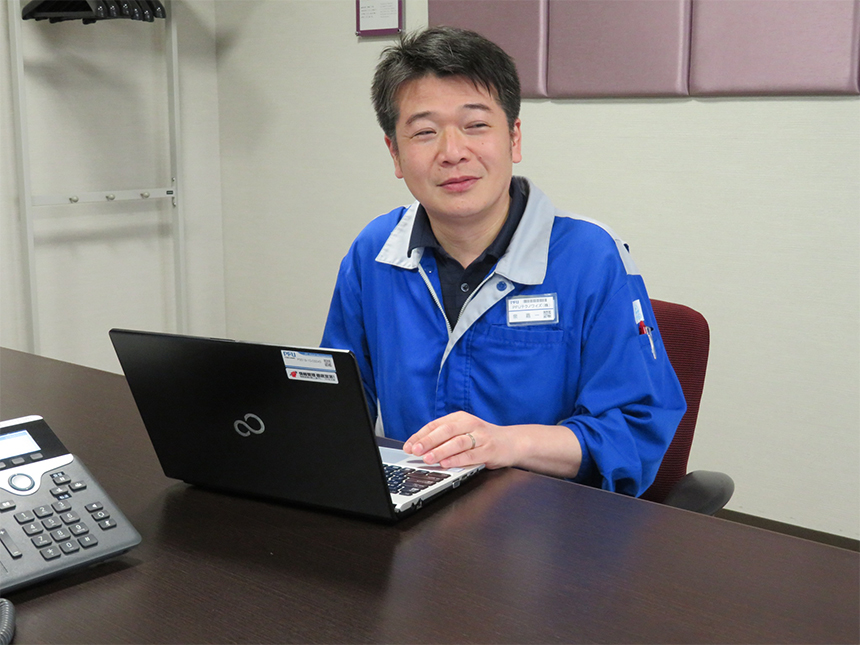
想定外の時間を要したものの、何とかその日のうちにライン再稼働にこぎつけたという。しかし、手放しで喜んでもいられない。大事なことは再発防止である。
"事件" の翌日からさっそく対策チームが編成された。PFUのネットワーク部門の担当者が現場に直接入り込んで、第三者の視点も交えて、まずは現状把握から始まった。
"事件" の翌日からさっそく対策チームが編成された。PFUのネットワーク部門の担当者が現場に直接入り込んで、第三者の視点も交えて、まずは現状把握から始まった。
これまでに実施していた対策
先にも述べたとおり、PTWではこれまでも現場の経験に基づき、「工場を止めない」ための対策をいくつか実施していた。例えば、以下のような対策である。
- 生産設備の管理の徹底
- 過去に発生したトラブル状況(何が原因でどう対処したか)の記録
- 工場内の機器の接続関係を示すネットワーク構成図の作成
見えてきた問題1:
工場全体を俯瞰する管理者が不在
当時実施していた対策のうち、「生産設備の管理」や「過去に発生したトラブル事例の記録」についてはどんな問題があったのだろうか。
これについては運用面での問題が明らかになった。つまり、記録はされているが共有が不十分といった点だ。
前者に関して実際に行われていたのは、あくまでライン単位での管理であり局所的な範囲にすぎなかった。言い換えれば、部分最適はされているが、自ラインを越えた状況把握まではなされていなかったということだ。 また、後者の「過去のトラブル事例」については、前任者から引き継いだメモは存在したが、トラブルの記録をルール化して共有するといった運用にはなっていなかったのである。
つまり、全ラインを統括する管理者が不在で、全体を把握できる状態になっていなかった点が、原因究明が遅れた要因の1つであった。
もっとも、こうした運用がこれまで問題にならなかった背景もあったようだ。製造技術部の堀氏は次のように話す。
「これまでは、ネットワーク障害が発生しても、その段階で原因や故障機器を目視で特定できるケースが多く、当該ラインの状況を熟知した担当者が対症療法的に最善の対処を行ってきた経緯があります。そのため、全体を俯瞰して管理できる人を専任でアサインする必要性を感じていませんでした」
これについては運用面での問題が明らかになった。つまり、記録はされているが共有が不十分といった点だ。
前者に関して実際に行われていたのは、あくまでライン単位での管理であり局所的な範囲にすぎなかった。言い換えれば、部分最適はされているが、自ラインを越えた状況把握まではなされていなかったということだ。 また、後者の「過去のトラブル事例」については、前任者から引き継いだメモは存在したが、トラブルの記録をルール化して共有するといった運用にはなっていなかったのである。
つまり、全ラインを統括する管理者が不在で、全体を把握できる状態になっていなかった点が、原因究明が遅れた要因の1つであった。
もっとも、こうした運用がこれまで問題にならなかった背景もあったようだ。製造技術部の堀氏は次のように話す。
「これまでは、ネットワーク障害が発生しても、その段階で原因や故障機器を目視で特定できるケースが多く、当該ラインの状況を熟知した担当者が対症療法的に最善の対処を行ってきた経緯があります。そのため、全体を俯瞰して管理できる人を専任でアサインする必要性を感じていませんでした」
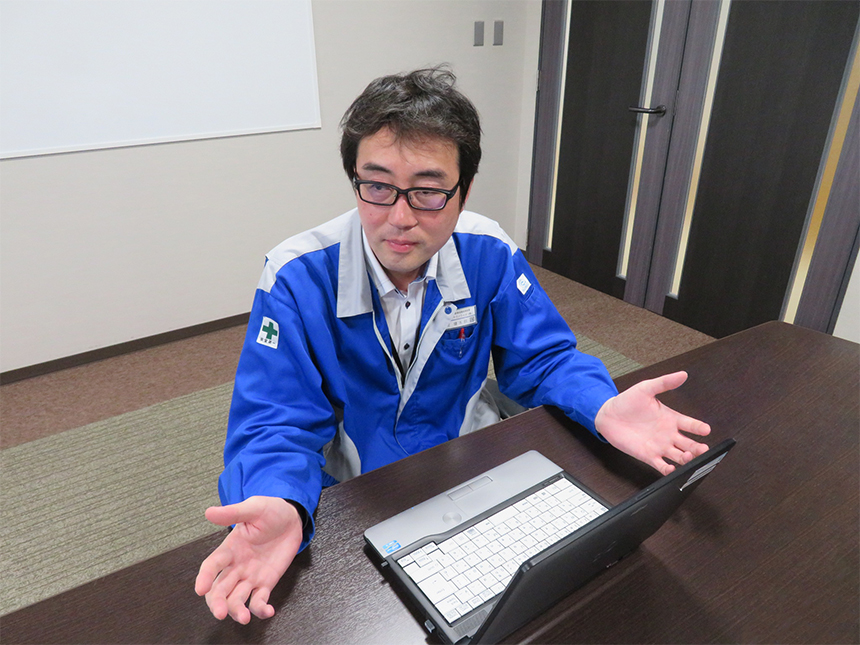
見えてきた問題2:
機器やネットワークの管理情報が最新化されていない
では、当時実施していたもう1つの対策、「機器の接続関係を示すネットワーク構成図」にはどんな問題があったのだろうか。
これについては、まず、当時運用されていた実際のネットワーク構成図を見ていただきたい。
HUBとそれに接続されているサーバーの関係がIPアドレスの情報とともに、製造ラインごとにキチンとまとめられていることがわかる。
これについては、まず、当時運用されていた実際のネットワーク構成図を見ていただきたい。
HUBとそれに接続されているサーバーの関係がIPアドレスの情報とともに、製造ラインごとにキチンとまとめられていることがわかる。
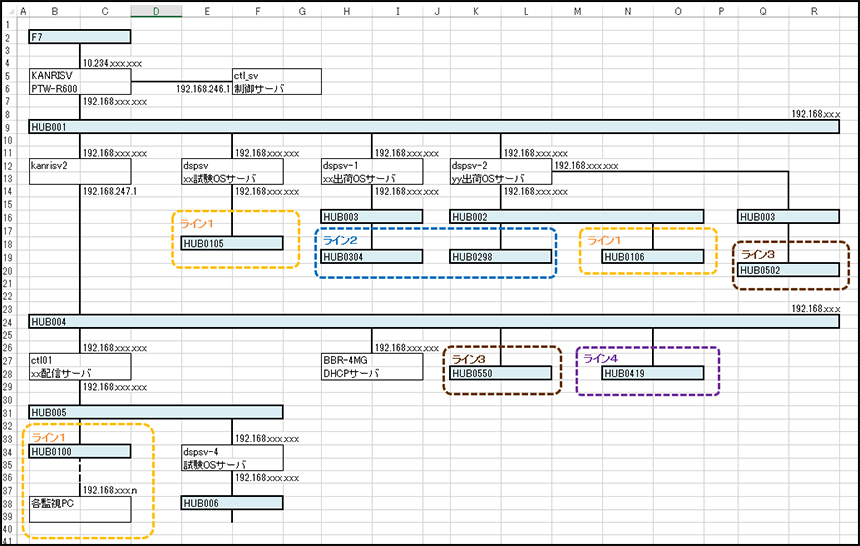
非常に丁寧に作成していることが見て取れるが、お気づきのとおり、表計算ソフトを利用して作成されている。使い慣れたソフトである点を割り引いても、手入力での作成と保守にはそれなりに時間を要することが容易に想像できる。
一方、工場では、季節によってあるいは生産計画に応じてレイアウトや生産ラインを変更することが高い頻度で行われている。こうした状況において従来の運用の何が問題かというと、現場のネットワーク構成と表計算ソフト上のネットワーク構成図との同期がとれていない(一時的に)ということ。つまり、最新化されていないということである。
せっかく時間をかけて作成しても、障害発生時の対策資料としてみた場合、最新化されていないことは致命的といえる。
一方、工場では、季節によってあるいは生産計画に応じてレイアウトや生産ラインを変更することが高い頻度で行われている。こうした状況において従来の運用の何が問題かというと、現場のネットワーク構成と表計算ソフト上のネットワーク構成図との同期がとれていない(一時的に)ということ。つまり、最新化されていないということである。
せっかく時間をかけて作成しても、障害発生時の対策資料としてみた場合、最新化されていないことは致命的といえる。
現場の声を反映して
生まれたiNetSec FC
見えてきた問題を整理すると以下になる。
(a) 工場全体を俯瞰する管理者がいない
(b) 機器とネットワークの管理情報が最新化されていない
(a) 項については、全体を管理するうえで求められる幅広いネットワークスキルを有した要員がいないといった課題も見えてきた。(b) 項については、最新化どころか、そもそも捕捉できていない機器が存在しているという課題も内在していた。 一般的に、こうした課題の解決には次のような対策が想定される。
しかし、品質・効率・稼働を最優先する工場においてはあまり現実的な対策とは言えない。工場という現場の事情と実態に、より即した対応が求められるからだ。
そこで生まれたのが、iNetSec FCだ。
iNetSec FCは、「増え続ける機器をカンタンに管理したい」、「ネットワーク構成を常に最新の状態で確認したい」、「ネットワークの専門知識がなくても使える製品がほしい」といった現場の声を反映して誕生した。
その誕生の背景にあるキーワードの一つが“見える化”である。
止まらない工場を実現する上で " 見える化" は、基本といえる。機器とネットワーク構成を見える化することで、万が一トラブルが発生しても対処が迅速に行えて、さらには、ネットワークの負荷状況を監視してリスクの予兆を捉えることで、トラブルを未然に防ぐ対応も可能になるからである。
(a) 工場全体を俯瞰する管理者がいない
(b) 機器とネットワークの管理情報が最新化されていない
(a) 項については、全体を管理するうえで求められる幅広いネットワークスキルを有した要員がいないといった課題も見えてきた。(b) 項については、最新化どころか、そもそも捕捉できていない機器が存在しているという課題も内在していた。 一般的に、こうした課題の解決には次のような対策が想定される。
- 教育による対応(ネットワークスキルの向上と人材育成)
- 体制の強化(専任要員を増強して管理情報の更新頻度を上げる=マンパワーで最新状態を維持する)
しかし、品質・効率・稼働を最優先する工場においてはあまり現実的な対策とは言えない。工場という現場の事情と実態に、より即した対応が求められるからだ。
そこで生まれたのが、iNetSec FCだ。
iNetSec FCは、「増え続ける機器をカンタンに管理したい」、「ネットワーク構成を常に最新の状態で確認したい」、「ネットワークの専門知識がなくても使える製品がほしい」といった現場の声を反映して誕生した。
その誕生の背景にあるキーワードの一つが“見える化”である。
止まらない工場を実現する上で " 見える化" は、基本といえる。機器とネットワーク構成を見える化することで、万が一トラブルが発生しても対処が迅速に行えて、さらには、ネットワークの負荷状況を監視してリスクの予兆を捉えることで、トラブルを未然に防ぐ対応も可能になるからである。
専門知識がなくても状況を
直感的に確認できる点に満足
PTWでの一連の検証を経て製品化されたiNetSec FC。そのiNetSec FCを導入した現在の運用状況を、具体的な効果とともに紹介する。
かつて、表計算ソフトで手入力管理していたネットワーク構成図は、iNetSec FCの導入によって、自動で作成されるようになった。これにより、「接続されている機器の情報や状況も含めてネットワークの構成をカンタン、確実、視覚的に把握できるようになった」(製造技術部 堀氏)という。もちろん、レイアウト変更に連動して、機器の接続構成も自動的にも反映されるため、常に最新の状況が確認できるようになっている。
かつて、表計算ソフトで手入力管理していたネットワーク構成図は、iNetSec FCの導入によって、自動で作成されるようになった。これにより、「接続されている機器の情報や状況も含めてネットワークの構成をカンタン、確実、視覚的に把握できるようになった」(製造技術部 堀氏)という。もちろん、レイアウト変更に連動して、機器の接続構成も自動的にも反映されるため、常に最新の状況が確認できるようになっている。
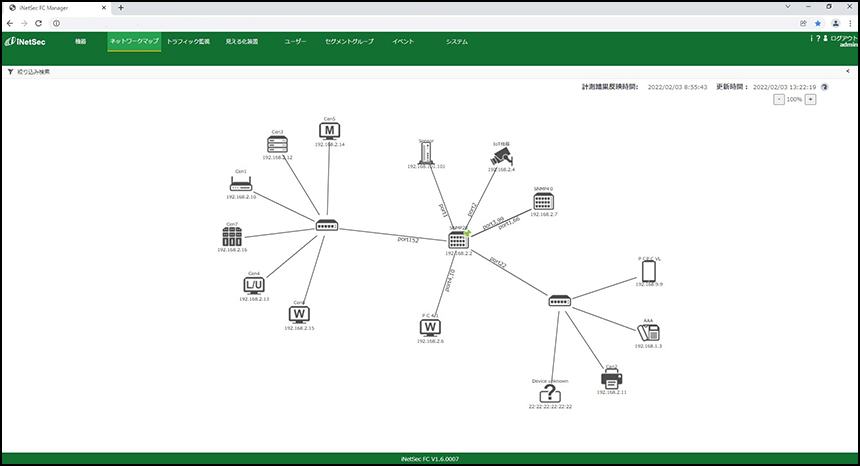
従来の運用に比べて、「接続されている機器の情報を直接、現物確認していた手間」、「レイアウト変更のたびに手作業でメンテナンスしていた手間」、「ケーブルをたどって接続関係を確認していた手間」が解消され、工数に換算すると約1.5人月程度の削減になったという。
「何よりも、トラブルが発生した場合に画面上で状況が確認できるので、原因の特定と対処が迅速に行えるという点が安心感という意味でも大きいですね。しかも、ネットワークの専門知識がなくても状況を直感的に確認できる点も現場としては助かっています」(経営管理部 濱名氏)。
「何よりも、トラブルが発生した場合に画面上で状況が確認できるので、原因の特定と対処が迅速に行えるという点が安心感という意味でも大きいですね。しかも、ネットワークの専門知識がなくても状況を直感的に確認できる点も現場としては助かっています」(経営管理部 濱名氏)。
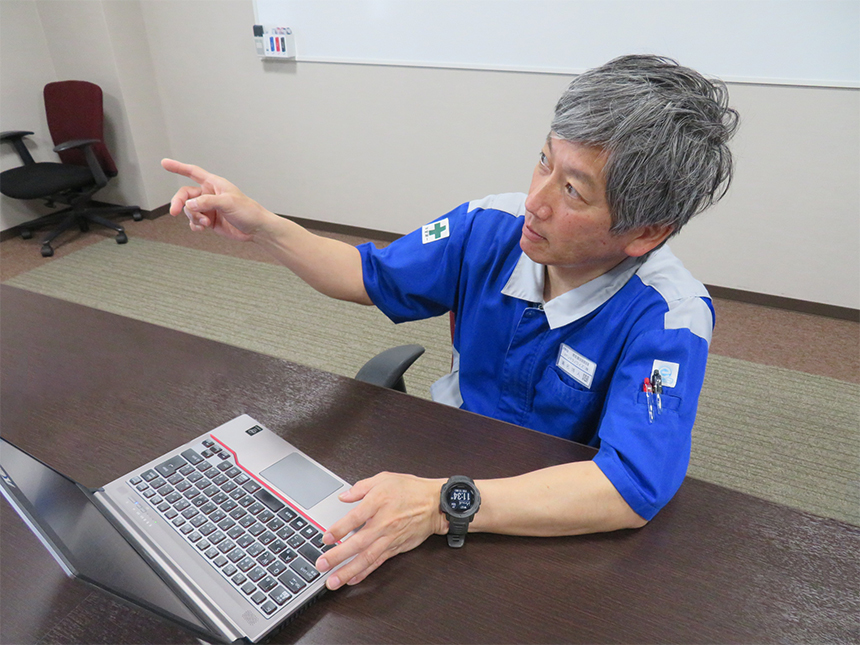
「PTWでは以前から、工場内の見える化に積極的に取り組み、PDCA改善に役立てています」
「進捗確認を目的とした生産計画の『予実の見える化』、リードタイムを把握するための『滞留状況の可視化』、部品供給が適切に行われていることを確認するための『ライン状態監視』などです。今回、iNetSec FCの導入により、機器とネットワークの見える化もラインアップに加わったことで、これまで懸案だった機器の接続関係と状況の把握がカンタンに行えるようになりました」(製造技術部 泉氏)。
現在は、これらの見える化の仕組みを束ねて、さながらコックピットに見立てて、工場全体を効率よく監視する運用を展開しているという。
「進捗確認を目的とした生産計画の『予実の見える化』、リードタイムを把握するための『滞留状況の可視化』、部品供給が適切に行われていることを確認するための『ライン状態監視』などです。今回、iNetSec FCの導入により、機器とネットワークの見える化もラインアップに加わったことで、これまで懸案だった機器の接続関係と状況の把握がカンタンに行えるようになりました」(製造技術部 泉氏)。
現在は、これらの見える化の仕組みを束ねて、さながらコックピットに見立てて、工場全体を効率よく監視する運用を展開しているという。
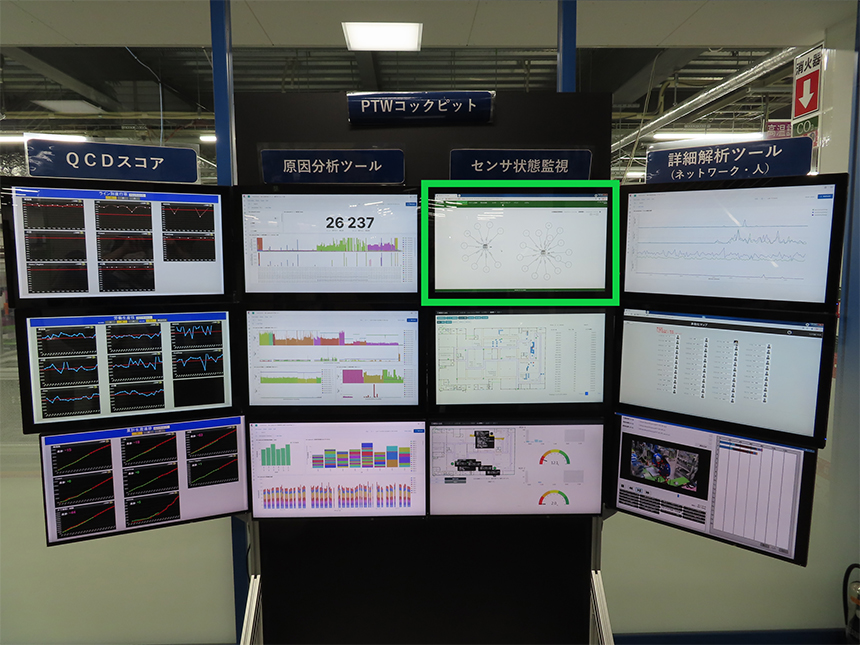
これからもiNetSec FCを
活用して「止まらない工場」を目指す
PTWにおける、iNetSec FCの導入事例について述べてきた。
PTWがかつて抱えていた課題が他の工場にもそのまま当てはまるとは限らないが、多くの工場でも同様の課題を抱え、悩んでいるのではないだろうか。また、自分の工場ではそれなりに対策は実施しているが、今よりも少しでも改善したい(可能ならできるだけカンタンに)と考えている人もいると思う。そういった方の想いに応えることがiNetSec FCの原点にあることは確かだ。
最後に、iNetSec FCに期待することについて伺った。
三人とも口を揃えて「私たちは、常に『止まらない工場』を第一に考えています。その意味で、現場が抱える課題を起点として誕生したiNetSec FCの機能には満足していますし、その効果も実感しています。さらに、今後新たな機能を追加する場合も、今回のように現場の声に耳を傾けながら開発されることを期待しています」と話してくれた。
PTWがかつて抱えていた課題が他の工場にもそのまま当てはまるとは限らないが、多くの工場でも同様の課題を抱え、悩んでいるのではないだろうか。また、自分の工場ではそれなりに対策は実施しているが、今よりも少しでも改善したい(可能ならできるだけカンタンに)と考えている人もいると思う。そういった方の想いに応えることがiNetSec FCの原点にあることは確かだ。
最後に、iNetSec FCに期待することについて伺った。
三人とも口を揃えて「私たちは、常に『止まらない工場』を第一に考えています。その意味で、現場が抱える課題を起点として誕生したiNetSec FCの機能には満足していますし、その効果も実感しています。さらに、今後新たな機能を追加する場合も、今回のように現場の声に耳を傾けながら開発されることを期待しています」と話してくれた。
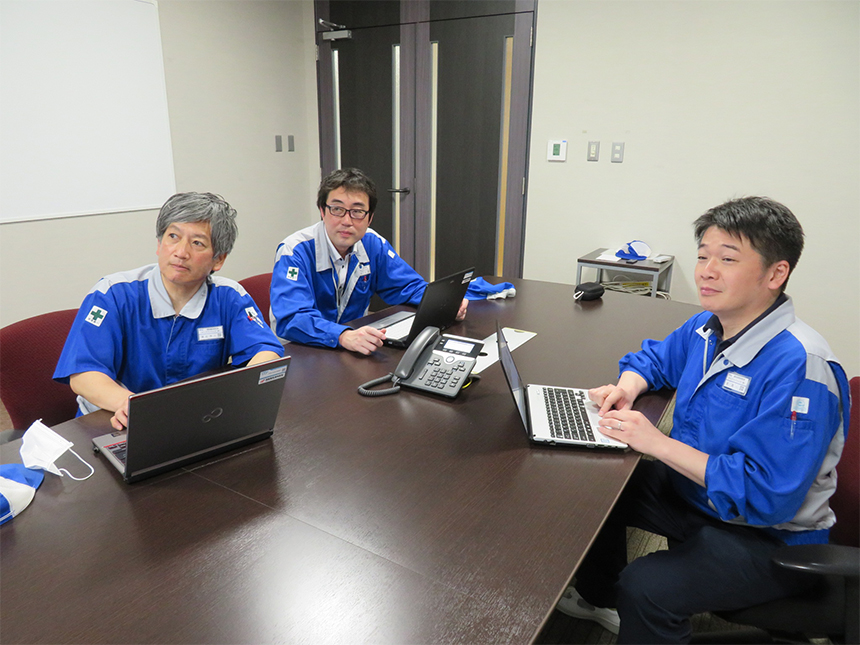
濱名氏(左)、堀氏(中央)、泉氏(右)
お客様概要
名称 | PFUテクノワイズ株式会社 PFU Techno Wise Limited. |
---|---|
所在地 | 石川県かほく市高松シ1番地1 |
操業 | 1979年 2001年 PFUテクノワイズへ社名変更 |
資本金 | 1億円 |
従業員数 | 200名(2021年4月現在) |
URL | https://www.pfu.ricoh.com/ptw/ |
活動概要 |
|
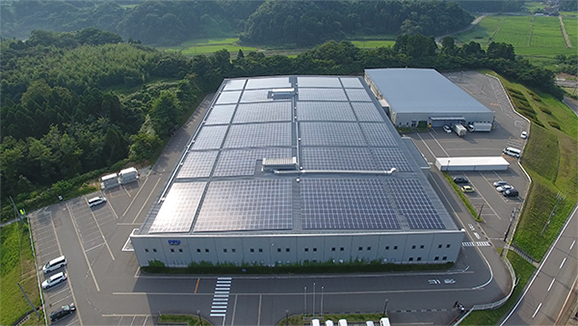
この事例で
ご導入いただいている製品
ご導入いただいている製品
- iNetSec FC
- 詳細はこちら!